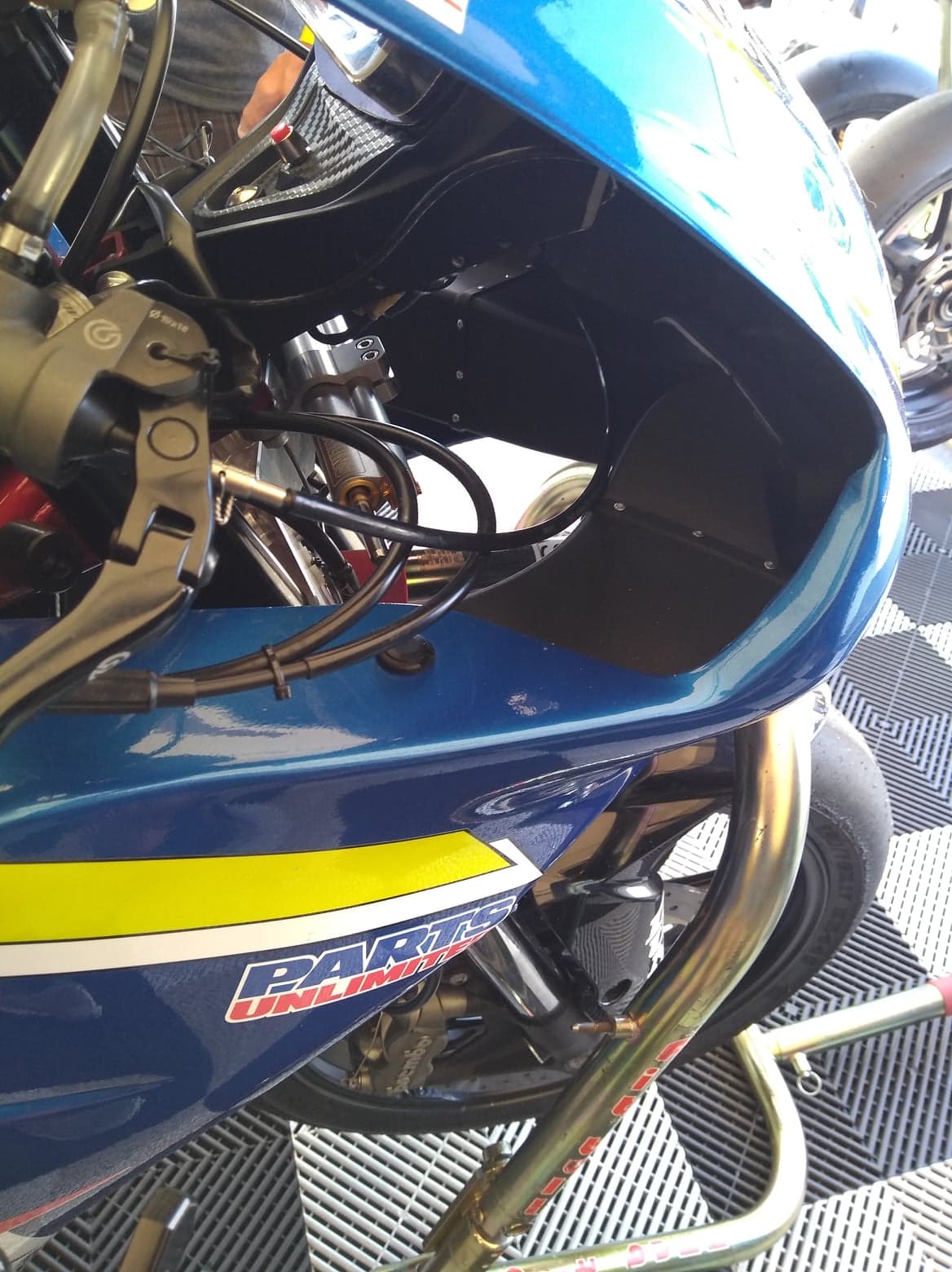
A few weeks ago, we did a story about CarbonSmith, which is a team sponsor of Westby Racing. Owned by Ryan Shaun Smith, the company creates 3D-printed components for various industries, including motorcycles. Several components on Westby Racing’s Superbike are 3D printed using a process called Continuous Fiber Fabrication.
After the story ran, we were introduced to Jason Heard and Jack Fisher, owners of Tekk Consulting, a company that is also heavily involved in the 3D printing industry. Tekk has worked with Team Hammer for the past couple of years, and we interviewed them as a follow-up to the story that we did on CarbonSmith.
The interview with Heard and Fisher is extensive, so we divided it up into two parts, and we still left a lot on the table as far as what’s currently going on in the 3D printing industry, and especially as it pertains to the MotoAmerica paddock.
Here is Part One of the interview:
Jason and Jack, let’s start by you telling us the name of your company and how it relates to MotoAmerica.
Jason:
We’re Tekk Consulting, and race teams, builders, and manufacturers come to us to provide them with parts and components solutions. We’re kind of like tattoo artists. They pick it, and we stick it. That’s our primary business.
We’re also the co-founders of a company called Philifi, which is the next generation of DIY or do-it-yourself 3D printing. We call it “PIY,” which stands for Print It Yourself. As it relates to the motorcycle industry, we own PIYauto.com which is a soon-to-be-launched digital asset marketplace for all things that are 3D printed in the automotive industry.
What we do have up and running is a smaller variant of that called DIYoffroad.com, which sells digital assets to the off-road motorsports community.
In the future, the industry as a whole is going to be intellectual property creators and independent/end users. For example, let’s say Jack designs a new set of bodywork for one of the new sportbikes. Let’s just call it the new “X-1000.” He can sell that digital asset to motorcycle shops, race teams, etc., who will to be able to print the bodywork just as Jack designed it. Or, they can purchase the digital asset from Jack, customize the design, and then print their own variation of Jack’s original design. That’s what we’re working towards. But, obviously, we have a lot of things to work through first.
One of those things is, how do you even 3D print motorcycle bodywork? A year ago, Jack and I started on this endeavor and initially we wanted to get people to make the printers for us. That didn’t pan out well. Long story short, we had to start from scratch, and we developed our own large-format, pellet-based FDM printers. The smaller of those printers are actually large enough to print complete motorcycle fairings.
On top of that, we’re also working with Team Hammer’s Chris Ulrich to get MotoAmerica’s approval, and the FIM’s approval, to allow 3D-printed fuel cells. Since we already have FIA approval to create 3D-printed fuel cells, the next step would be getting FIM approval, and we just submitted all the documentation for that a couple of weeks ago.
A lot of these types of things are rapidly changing, and not just on the racing side of the motorsports and powersports industries, but in those industries as a whole, whether it’s motorcycles, ATVs, UTVs, cars, trucks, etc.
We recently published a story about a company called CarbonSmith that makes 3D printed parts. In the story, we implied that this is emerging technology in the motorcycle road racing industry, and certainly in the MotoAmerica paddock. We received some comments on our Facebook page saying that 3D printing is not emerging technology because it’s been around for over thirty years. Sure, 3D printing has been around for more than three decades, but it is still emerging technology in our particular sport. You underscored that with what you just said. So, just to reiterate, would you say that 3D printing is emerging technology in the MotoAmerica paddock?
Jason:
Yes. At the most, it’s only been around for just the past few seasons. Two to three seasons max would be my guess. A lot of it has to do with industry norms and costs. There are lots of ways to create some really cool motorcycle parts right now with 3D printing. But, whether or not it’s viable from a cost standpoint, a lot of it is just not there yet. But it’s moving rapidly in that direction.
Jack:
From another angle, it’s also about the ease of printing. You can buy printers now for as little as $150, but every time you use them, it’s a science experiment in itself to get them to work successfully. Companies like Markforged, when they showed up on the scene, they were really bringing forward the concept that “Here’s a desktop 3D printer that you can print usable parts on.” I think we had to reach a point where the machine could do it by itself without a ton of user knowledge in order for it to really start to, number one, be trusted, and number two, work successfully.
In the story about CarbonSmith, we learned that they use Continuous Fiber Fabrication with carbon fiber and resin, which provides some dimensional stability in the 3D-printed parts. Ryan Shaun Smith told us that he makes parts like fairing brackets and coolant pipes and things like that, but when it comes to 3D printing of parts like suspension linkages, he prints a prototyping piece that is eventually made out of CNC-machined billet. Can you please touch on the idea of printing parts out and putting them right on the bike versus printing out a prototype that’s going to be fabricated into a usable part later on.
Jason:
First and foremost, what you are referring to is Onyx filament. That’s what Markforged uses in their series of desktop 3D printers. And what you’re referring to as continuous fiber, well, that technically doesn’t exist with Markforged printers. Even Markforged uses that sort of terminology, and it’s technically incorrect. It’s not continuous because every single layer has a break in the material.
Jack:
There’s a company called Mantis Composites that has created their own in-house, five-axis, 3D printer. If you want to actually achieve the strength of the fiber, it’s all about the tensile direction that is getting pulled on. Machines like Markforged use a standard plastic that’s got chopped carbon fiber in it. It is an additive particle that helps to stiffen the base plastic. Then, after one layer is printed, it comes back and extrudes a strand of either fiberglass, high-temp fiberglass, Kevlar, or carbon fiber, and embeds it into the layer of plastic, with or without chopped carbon fiber to help stiffen that layer. But you’re only going to see that achievable strength in the two axes, or the plane that it’s being put into. The five-axis 3D printing technology created by Mantis Composites allows you to actually put the fiber in the direction you need it.
Regarding chopped carbon fiber, as we understand it, it’s printed in a pattern that creates some inherent strength or stability, even though it’s not literally a continuous filament throughout the printed piece. One of the things that CarbonSmith showed us was a right-angled coolant pipe. Ryan Shaun Smith actually wrapped some filament around the elbow to create additional strength in that section of the part.
Jason:
Exactly. Mantis is one of the few companies actually printing continuous carbon fiber, and the only companies that can even remotely afford those types of printers are Lockheed Martin and Boeing. It is insanely expensive right now, and no one in the MotoAmerica paddock can afford it, unfortunately. At least not yet.
We’ve had Markforged printers for a while now and, as far as usability of the parts that are printed with it, it is a bit of a slippery slope. We have a bunch of stuff that we 3D printed for Team Hammer that is usable. But nothing like a suspension link or anything along those lines. The material and the processes aren’t quite there yet to where you can 3D print and install those kinds of components right on the bike. There are printers that can make the components out of various metals, but again, it’s too expensive and time-consuming for the time being.
Jack:
3D printers that can produce metal parts that are usable incorporate a process called Direct Laser Sintering. The process utilizes a metal powder that is melted layer by layer into the final shape. There are also Fused Deposition Modeling 3D printers that print a metal powder bound in wax, which you then sinter into a final solid part. The third method for metal printing is essentially a welding torch replacing the hot end for plastic. Those are the common current ways that you can 3D print metal in a usable form.
Also, there are only a limited number of metals that you can currently 3D print with, correct?
Jason:
Yes, currently. A good example of this exists in the supercar market. We are starting to see implementation of 3D metal printing in certain types of intake manifolds, turbo setups, etc. It’s usually only seen on high-end Audis, Lamborghinis, Porsches, etc. Those customers are accustomed to spending $15,000 for an exhaust system. Components that are difficult to create in a CNC milling machine, for example, are 3D printed. Certain sections of the exhaust manifold and other connections that are organic in shape. But, again, the cost of the overall exhaust system is so expensive that they can actually incur the 3D printing cost without it being prohibitive.
That’s kind of the only usable route for 3D metal printing at the moment, until it becomes less expensive. But, every year, it’s getting cheaper and cheaper to 3D print things out of metal.
Now, as far as usable parts on a race bike, I think we’re still a few seasons out before we start seeing 3D-printed metal components in the MotoAmerica paddock. But, as far as composite-based components, Jack and I have been working on a quite a few different things. We did a bunch of stuff for Team Hammer last season, especially with their SV650 Twins Cup program. The Twins Cup bikes that Alex Dumas and Joseph Blasius raced had 3D-printed air intakes on them along with some other parts that we were working on to create performance gains.
Jack:
And we were successful.
Yes, it worked out pretty well, with Alex Dumas winning the Twins Cup Championship.
Jack:

Proper design and implementation offer so many advantages. The season had already started, and Team Hammer needed a better solution for the air intakes on their bikes. Because of 3D printing and our rapid design process, we were able to implement a solution fast enough to help them win.
They certainly had an amazing season. Those Team Hammer bikes were incredible in so many ways, not to mention that they had a topnotch rider. It sure was proof of concept for your 3D printed parts, though, wasn’t it?
Jason:

Yes, and here’s how it started. We went to COTA, and I actually scanned the bike right there in the paddock with our 3D scanning equipment. We have all the 3D scanning equipment and are able to do that virtually anywhere. So, I scanned the bike and sent the data over to Jack who was in California. He processed the 3D scan data and started drawing all the new pieces within a day or two. Then, within a week, we had prototypes printed and by week two or three, we had the production set of parts for Team Hammer. The set consisted of a mixture of both chopped carbon fiber parts off the Markforged printer, and parts that were a little bit more flexible. The set is a combination of different 3D-printed components that go together as one unit.
Jack:

To be clear, in that situation, the prototypes themselves were not just a matter of “3D-print the parts, check the fit, and machine on a CNC.” It was actually “cut the air box here, insert the parts, attach these pieces, go out on the track, do some laps, see how everything performed.” But, in that specific application, it was usable prototype parts from day one.
Can you talk a little bit more about your ability to scan an entire motorcycle? How do you do that?
Jason:
For this application, I have a laptop that has the software on it, and we have a 3D scanner. So, it’s mobile. I flew out to COTA with my equipment, and we set it up right there in the paddock. First, I scanned the entire front fairing of the bike, then we pulled the fairing off and scanned the bike again. Then I scanned both the inside and outside of the fairing separately. Then we converted all of those scanned data files to solid files that we aligned together. From there, Jack was able to design an entirely new intake assembly that actually followed and mimicked the fairing and the bodywork. So that’s how we were able to get all the data collection to properly draw all that. Now, when it comes to very critical measurements or parts, we always double- and triple-check everything by hand. So that means using measuring tools like calipers and referencing points A, B, C, D, etc.
I’m used to scanning a two-dimensional piece of paper. You just put it on a flatbed scanner and press the button. How do you scan a three-dimensional part?
Jason:
We use a freeform scanner that takes a ton of data points–we’re talking millions per second–and creates a three-dimensional point cloud in the computer. You just sweep over the structure, and it grabs hundreds of millions of three-dimensional points that the software then uses to reference itself, and then aligns all that into a three-dimensional structure in the computer.
Jack:
It captures the texture of the part, too.
Jason: The stuff we have isn’t necessarily the most advanced or newest when it comes to 3D scanning, but five years ago, it didn’t really exist to where guys like us could do this stuff at a racetrack and then draw the part from the data within a day or two. You used to have to do everything by hand. Or in these situations, it would be like trying to beg Suzuki to give us OEM files, which for obvious reasons is essentially impossible. A lot of the OEMs do not want to give out any of this data, so it forces guys like us, and the race teams, to do things the old-fashioned way. A lot of tape measures. A lot of guessing and double-checking. Making parts and seeing if you’re close, then remaking the parts. You may have to print multiple revisions of something just to get in the ballpark to start drawing the final part. But, with 3D scanning, we eliminate a lot of that stuff to where we’re going from nothing in the computer to final drawing of the piece within days.
Next Week: Part Two of the interview where Jason and Jack discuss 3D printing of motorcycle bodywork.
To purchase tickets for all MotoAmerica events, click HERE
For information on how to watch the MotoAmerica Series, click HERE
For the full 2020 MotoAmerica Series schedule, click HERE